Wireless
Vibration Monitor PCE-VMS 504
wireless vibration monitor with external
vibration sensors/
to measure acceleration, speed, offset and temperature /
optional extension: max. 60 dispatchers per base with max. 6 base stations (360 dispatchers)
|
The
wireless vibration monitor PCE-VMS 504 detects vibration within an acceleration
range of up to 30 g and a frequency range between 5 and 10 KHz. The wireless
vibration monitor therefore features external vibration sensors, which measures
vibrations at machines to transfer those wireless to a receiving unit. Those
sensors can be easily attached to a machine due to its magnetic base. There they
can not only measure vibrations at machines and transfer those to a computer but
also recognize temperatures between -20 and +120 °C. While operating, the
communicating server of the wireless vibration monitor PCE-VMS 504 sends the
measured parameters straight to a receiving unit, which then uploads the
received data straight to a server. But if the system cannot establish a
connection with the server, the parameter are temporarily saved on the receiving
unit until a server-connection could be re-established. A main advantage of the
wireless vibration monitor is that there are no wires, so that the set-up of the
system is much quicker and easier, while the wireless vibration monitor is able
to record vibrations over a longer period of time. If there are any questions about this
Wireless Vibration Monitor PCE-VMS 504, please
have a look at the technical specification below or call: UK customers +44(0) 23 809 870 30 / US customers +1-410-387-7703. Our technicians and engineers will gladly advise you regarding all vibration
monitors and all products in the field of measuring
instruments, regulation
and control and scales.
|
|
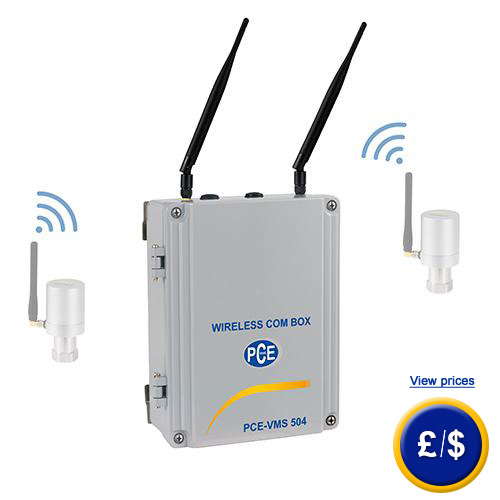
|
- Wireless communication via ZigBee
- Frequency range between 5 Hz and 10 kHz
- Wireless transferring Piezo sensors
- Large radius of coverage
- Can be extended at any time
|
-
Dispatcher IP 65 protected
- Temperature measurement up to 120 °C
- Data memory (receiving base) 128 MB
- Long battery lifetime
- No extensive wiring required
|
Technical Specifications
of the Wireless Vibration Monitor
|
Communication
type
|
ZigBee
(with PCE-VMS 501)
ethernet, glass fibre cable, wireless (with server)
|
Frequency
band
|
2.4
GHz
|
Interfaces
|
Ethernet
2.0 IEEE802.3, TCP/IP, 10/100baseT
|
Data
storage capacity
|
128
MB
|
Power
supply
|
220
VAC or POE
|
Operating
temperature
|
-20
... +50 °C
|
Dimensions
|
250
x 210 x 100 mm
|
Weight
|
2400
g
|
Technical
Specifications about dispatcher of the Wireless Vibration Monitor PCE-VMS 504
|
Dispatch
range
|
max.
100 m in industrial environment
(130 m in free field)
|
Acceleration
range
|
up
to 300 m/s²
|
Frequency
range
|
5
Hz ... 10 kHz
|
Resonance
frequency
|
16
kHz
|
Linearity
|
1
%
|
Sensitivity
for paramaters that are not relevant for measurement
|
≤5 %
|
Electric
insulation
|
<108
Ω
|
Load
limit
|
1000
g
|
Measuring
parameters
|
Acceleration,
speed, temperature, offset
|
Dispatch
interval
|
min.
1 minute per sensor
1 sensor at 1 box = 1 minute
3 sensors at one box= 3 minutes
|
A/D
conversion
|
24
Bit
|
Measurable
range for wave form
|
max.
512 kB
|
Frequency
lines
|
800,
1600, 3200, 6400
|
Measurement
range for temperature
|
-20
... +120 °C
|
Screw
thread
|
6
mm
|
Material
of enclosure
|
Bottom
316 L stainless steel,
top aluminum alloy
|
Power
supply
|
1
x 3,6 V lithium battery (ER 34335)
|
Battery
lifetime
|
1
year, depending on transfer interval
|
Dimensions
|
height:
80 ,
diameter: 40 mm
|
Weight
|
217
g
|
Protection
class
|
IP
65
|
Operation
temperature
|
-30
... +70 °C
(Surface temperature up to 125 °C)
|
Receiver
of wireless vibration monitor PCE-VMS 504
|
|
The
receiver station of the wireless vibration monitor PCE-VMS 504 is the connection
between vibration sensors on the machine and the analysis software MOS2000
installed on a server. After receiving the data about the machine, the receiver
dispatches those information via Ethernet to an internal or external server. The
power supply is 220 V, but can be effective via POE as well.
|
Vibration
sensor of the wireless vibration monitor PCE-VMS 504
|
|
The
vibration sensor of the wireless vibration monitor can record the oscillation
path, oscillation speed and the oscillation acceleration. In addition to these
parameters regarding oscillation the wireless vibration sensor can also measure
temperatures to a maximum of 120 °C. Due to protection class IP65 the sensors
also record reliably the machine data in humid or dusty environments. The sensor
not only collects the data but also dispatches those. Depending on the
surrounding conditions the sensor is able to send those data over a distance of
up to 100 m or even more. The power source of the sensor is a 3.6 V set of
batteries with a lifetime of more than a year (depending on the data transfer
interval ). The sensor can be coupled in various ways. The wireless vibration
monitor features a M6 thread inside the receiving base made of steel. Through
the thread you can for example connect the sensor via a stud screw to the
oscillating source. The coupling can be performed via a magnetic or a attachable
adapter as well.
|
Application
of the oscillation analysis software MOS2000
|
|
Analysis
of oscillation and vibration via the analysis software MOS 2000
|
The
wireless vibration monitor works with a software called MOS 2000, which provides
analysts an efficient program for diagnosis and general evolution of the
machines' performances according to ISO10816. The software is based on a browser
and can be accessed via web. Thus the data can be accessed worldwide. Thus
different branches of an industry can be accessed and monitored at the same
time. And the analyst does not even need to be on site.
|
You
can set up different user profiles at the software, each of which can have their
defined access rights. Thus there can be reports generated from the accumulated
data sets, transfer intervals can be set or alarm thresholds for borderline
oscillation parameters can be defined. On the analysis software of the wireless
vibration monitor each production site can be shown in a model of the actual
original and be occupied with a measuring slot. Those measuring slots are
accordant to the actual vibration sensors on the machine. The measurement slots
can be defined regarding the oscillation path, speed and acceleration. Furthermore
the frequency range which shall be measured by the vibration sensor, can be
defined for each measuring slot individually. Each measuring slot can display a
maximum of 3 oscillation parameters. For a further understanding of how to
configure a ,measuring slot an example is given in the following:
|
Oscillation
speed:
|
v
[mm/s] frequency range: f [10 Hz - 1 kHz]
(parameter to determine the oscillation intensity according to ISO 10816)
|
Oscillation
acceleration:
|
a
[mm/s2] frequency range: f [10 Hz- 10 kHz]
(broad analysis of the whole spectrum)
|
Oscillation
acceleration
|
a
[mm/s2] frequency range: f [2 Hz- 2000 Hz]
(Checking the low frequency range via analysis of the envelope to cover damages
on ball bearing or gear wheels)
|
The
relevant recorded data are transmitted by the vibration sensor via ZigBee to the
receiver base (PCE-VMS 504) and permanently saved on the connected data server.
With the software MOS2000 the relevant measuring slot can be reviewed and the
results according to the configured parameters can then be read-out with almost
real-time speed. The generated data sets are then stored purely as oscillation
values in MOS 2000. With that software a variety of analysis tools can be then
applied.
By
means of the analysis software MOS 2000 a detailed prognosis about the quality
of the ball gearing' components can be developed afterwards. Many vibration
meter often cause a reduced quality and an abrasion on the elements of the
machine on which the vibration meter is applied, due to their measuring method,
e.g. if a sensor-resonance is measured with the units BCU, SPM etc. That method
also does only allow good/bad decisions but no detailed analysis about the
magnitude of the damage on outer or inner ring, rolling body or retainer. Since
a databank of the rolling body is often integrated by most manufacturers the
theoretical damage frequency shown there can be compared to the actual measured
oscillation frequencies. Tools, which the MOS 2000 can pick from, are for
example: time signal, frequency analysis, waterfall diagram, cepstrum, envelope
analysis etc.
|
Time
signal:
The
time signal shows the offset (s[µm]), speed (v [mm/s]) or acceleration (a [mm/s2]
[g]) of a measuring point from its position of rest over time. The relevant
deflection is defined by its amplitude, frequency and phase angle. A common
example therefore is a harmonic sinusoidal oscillation. In reality there are
often periodic values throughout the time signal, but since in most cases they
are oscillation compounds with a basic oscillation and several high frequency
oscillation components, those signals must be demounted for further
analysis.
Frequency
spectrum:
The
frequency spectrum originates from a Fast-Fourier- Transformation of the time
signal. The FFT integral demounts the temporal periodic oscillation into
its harmonic oscillation parts and displays the relevant amplitude on a
frequency axis. The width of the frequency axis an therefore the measurable frequency
range covers in theory 0 Hz to Nyquist frequency, which is half of the sensor's
sampling frequency. I.e. to display a frequency of 10 kHz the signal has to be
at least sampled with a 20 kHz frequency. Therefore the determined frequency
amplitudes allow conclusions about defect our faulty machine parts.
Waterfall
chart:
The
waterfall chart displays the frequency spectrum in a three-dimensional form. In
addition the z-axis can be assigned with further parameters e.g. revolution,
performance or operating time. The vibration monitor visualizes in the z-axis
the chronological sequence of the spectral allocation of oscillation. Due to
this 3-dimensional visualization amplitude fluctuations or offsets of frequency
bands can be shown easily.
Cepstrum:
The
cepstrum analysis is another parameter for detailed analysis of harmonic
correlations over the spectral oscillation distribution. The Cepstrum analysis
helps detecting quefrencys. Quefrencys are frequency parts which are not recognizable
in a pure spectrum. The Cepstrum analysis is a reliable method to monitor gears,
since due to the interlock of various waves and gear-wheels there is a cinematic
correlation between all of its components.
Envelope
analysis:
The
envelope analysis helps uncovering impulse patterns. Those pulse patterns can be
caused by faulty gear parts or gear-wheels. Compared to the whole oscillation
image within the frequency range of a machine, the amplitudes of those pulse
patterns are relatively small and often not distrainable from the general
noise. Only the natural frequency of the stimulated components is recognizable.
To display the causing pulse patterns the oscillation signal is driven through a
bandpass filter, alignment of peak values and a following FFT analysis of the
envelope analysis. For an evaluation of the gear-wheels the envelope analysis is
an important parameter, since its facilitates detecting pulse patterns that
would not be visible in a common spectral analysis of the vibration.
|
Delivery
Content of the Wireless Vibration Monitor PCE-VMS 504:
1 x Wireless Vibration Monitor PCE-VMS 504 receiver base,
1 x Monitoring-Software, 1 x adapter (1.5 m), 1 x adaptr cable (1.5 m),
4 x screws to attach to wall, 1 x instruction manual
|
Optional
Equipment of the Wireless Vibration Monitor PCE-VMS 504:
|
PCE-VMS
501
|
Oscillation
sensor, magnetic feet Ĝ 20 mm),
antenna (L=90 mm),
incl. set of batteries (lifetime 1 year)
|
PCE-VMS
AD1
|
Adapter
for pipelines (Ĝ 100 mm)
|
PCE-VMS
AD5
|
Adapter
for pipelines (Ĝ 500 mm)
|
PCE-VMS
AD10
|
Adapter
for pipelines (Ĝ 1000 mm)
|
SG-527
|
Glue
for metal to attach adapter
|
PCE-VMS-PC
|
Server
for monitoring software / supervision of data bases (necessary, if customer
hasn't already its own server)
|
PCE-VMS-CAL
|
Calibration
certificate (1-point initial calibration by manufacturer), per uniaxial sensor
|
PCE-VMS-CAL2
|
Calibration
certificate (1-point recalibration by manufacturer), per uniaxial sensor
|
Optional
Service for Wireless Vibration Monitor:
|
PCE-VMS-IB
|
Set
up of monitoring system
|
PCE-VMS-SV
|
Maintenance
on site
|
PCE-VMS-FW
|
Monitoring
remote desktop maintenance (for analysis of oscillation graphs or oscillation
data)
|
|
|
Similar
products to the Wireless Vibration Monitor: |